从Form 3到Form 4:臻墨以3D打印革新劳保与声学定制化生产流程
在工业制造和消费电子领域,3D打印技术正成为推动生产方式变革的重要力量。作为一家深耕定制化耳塞、耳机的高科技企业,臻墨通过Formlabs的Form 4 3D打印机,在劳工防护和声学定制化产品方面取得了显著突破。
定制化耳塞劳工防护:全时佩戴的舒适守护
在高噪音环境下,听力防护产品不仅需要有效阻隔噪音,更要满足长时间佩戴的舒适性需求。无论是批量生产的发泡棉耳塞、还是头戴式的耳罩,都无法解决长时间佩戴下的舒适性问题。这也导致了许多的工人在佩戴耳塞1~2小时后就会摘下来或者“虚戴”,耳塞就无法达到应有的听力防护。
针对这一情况,臻墨基于Form 4的3D打印技术实现了定制化耳道耳塞,以树脂材料打印,确保产品贴合耳道。定制化耳塞首先解决了传统耳塞因为不舒适,员工“取戴频繁”所导致防护减少的问题。在这一基础上,臻墨的团队也开发了符合人体工程学的相应设计,能够直接固定住整个耳甲腔,比批量生产的产品更好的达到防护。
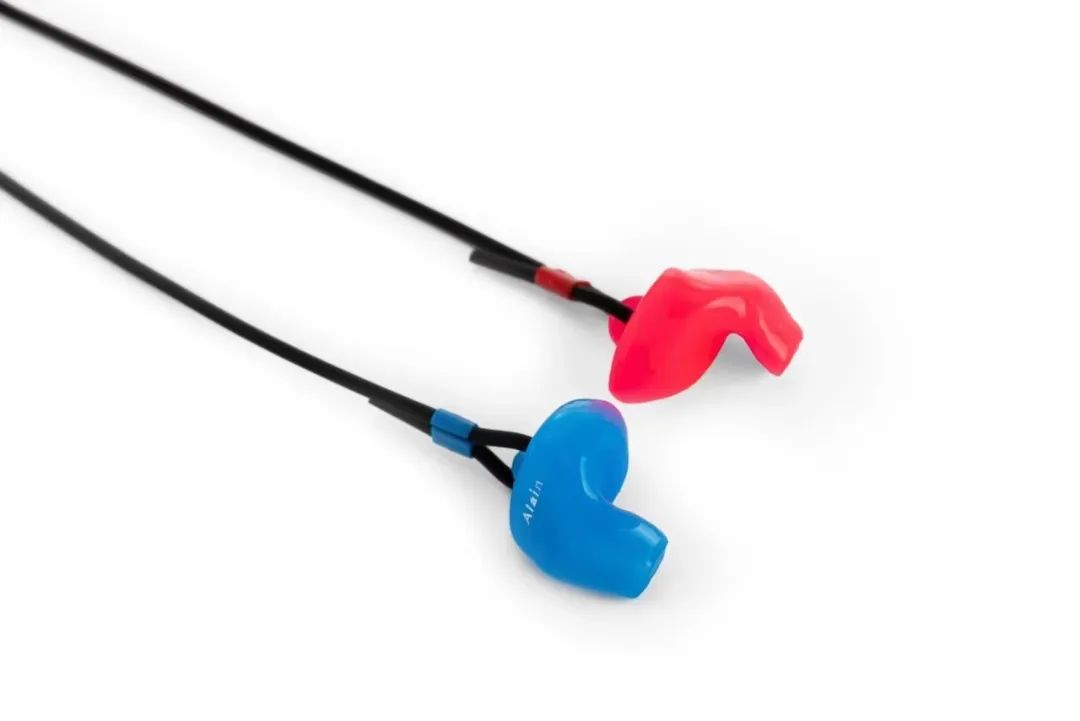
“如果产品不舒适,员工则无法全时全程佩戴。我们发现用Form 4打印出来的耳塞很舒适,很适合长时间佩戴,保证了工人佩戴耳塞的使用。”
—— 刘星宇
苏州臻墨健康科技有限公司CEO
Form 4提供成熟的3D打印定制成品
在定制耳塞的生产中,Form 4 3D打印机让个性化设计和生产变得便捷。臻墨将用户耳道的精准数据输入设计软件,再利用3D打印技术直接生产耳塞产品,不再需要开模和多次试验。打印完成后,通过简化的后处理工艺,产品即可快速进入终端应用。
这种方式不仅显著缩短生产周期,还能根据客户的特殊需求实时调整设计,为工业劳保产品和音乐耳机设备提供高质量、高精准度的定制化服务,极大地提高了终端产品的使用体验。
臻墨定制耳塞生产流程
1需求评估
确定客户需求及所需定制产品的数量、功能(如降噪、音质等)。
2耳道取样
针对定制耳塞,采用工具采集用户耳道形状数据。对于大型客户,可派遣现场团队进行取样或通过合作网点完成取样。
3数据建模
使用3D扫描仪将耳道模型数字化,导入设计软件,根据客户要求进行功能优化设计(如声学处理或防护性能调整)。
43D打印
使用Form 4 3D打印机打印产品初坯,以Clear Resin V5进行打印。
5后处理
对打印件进行打磨、抛光、喷涂或镭雕等处理,以提高外观和触感。
6性能测试
对产品进行功能性和耐用性测试,确保符合客户要求。
7包装与交付
产品完成后,打包发货,确保准时交付至客户手中。
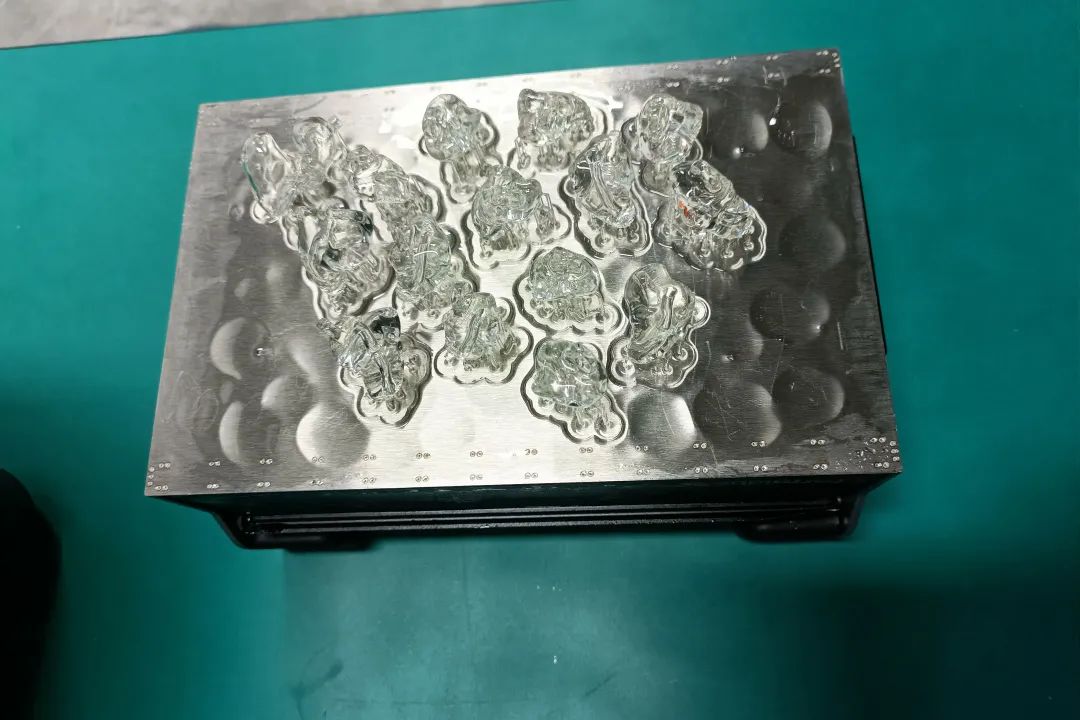
刚从Form 4中取下的打印件。
经过一系列后处理之后,3D打印的成品也能直接作为终端产品使用。
从探索到精通:臻墨的3D打印学习之路
得益于Formlabs对3D打印的洞察、Form 4成熟的工作流程和完善的前处理后处理系统,臻墨的生产团队很快就掌握了Form 3和Form 4的打印流程。但在如何把3D打印融入自己的产品开发和生产流程中,成为了摆在臻墨生产团队面前的难题。
从Form 3到Form 4:技术升级助力应用拓展

Form 4 更大的打印平台和更快的打印速度,让臻墨可以在一次打印中完成更多零部件的生产,同时保持与Form 3一致甚至更高的精度。据臻墨的技术总监金国星介绍,采用Form 4以后,他们每次可以打印约50件产品,打印时间也大大缩短至大约1小时,算上后处理的时间,生产效率提高了约3倍。在打印效率提高的情况下,打印精度也较之前采用Form 3时有了较大的提高。密集排版的情况下,产品的误差极小,打印成功率高。之前在密集排版下个别位置可能出现误差的情况,在Form 4的使用中也并未出现。
这种技术升级帮助臻墨在应对紧急交付需求和大规模订单时表现得更从容,在2024年年末,臻墨就接到国内一个工厂的劳保耳塞订单。有了Form 4打印系统的帮助,臻墨的技术团队仅用了两天时间即完成了从采集数据到交付26套耳塞的生产任务,赶在年末放假前完成交付,很好的展现了臻墨在3D打印生态的支持下所展现出的强大生产能力。
在材料适配性方面,Form 4延续了Form 3对多种树脂材料的支持,同时通过简化材料切换流程,进一步优化了生产效率。这种从Form 3到Form 4的技术演进,不是简单的替代,而是为企业生产模式的灵活性和扩展性提供了更多选择和可能。
期待3D打印材料与技术的更多可能性